L’evoluzione è una costante per l’intero settore aerospaziale, fin dai suoi albori.
Un’evoluzione mai fine a se stessa, ma fondamentale per soddisfare le sempre più stringenti necessità imposte dall’esterno. L’obiettivo, oggi, è creare mezzi sempre più efficienti e con minori consumi, per limitare l’impatto ambientale oltre che i costi.
Tale processo evolutivo rappresenta una sfida di proporzioni sempre più importanti per i produttori dei materiali metallici utilizzati in applicazioni aeronautiche e spaziali.
Si prendano come esempio i motori a reazione, che operano in ambienti estremamente ostili, caratterizzati da temperature elevate, dalla presenza di agenti corrosivi, da forze centrifughe, attrito, pressioni elevate e cicli di fatica intensi.
Oppure si pensi a componenti strutturali, come la cabina dell’aeromobile, i carrelli d’atterraggio o i rivetti di fissaggio, ai quali sono richieste prestazioni senza pari, in condizioni caratterizzate da repentine variazioni di temperatura e stress prolungati.
Il tutto garantendo non solo grande efficienza, ma anche la massima affidabilità e sicurezza operativa.
Per soddisfare requisiti di tale portata, diventa essenziale poter fare affidamento su materiali ad alte prestazioni, leghe metalliche e leghe speciali appositamente progettate.
Tali materiali devono quindi:
- dimostrare una straordinaria resistenza alle alte temperature
- avere la capacità di resistere alla corrosione e all’ossidazione
- offrire un eccezionale rapporto tra peso specifico e resistenza meccanica
- vantare una grande durabilità.
Classificazione delle leghe metalliche e leghe speciali per l’aerospace
A seconda del tipo di applicazione, nel settore aerospaziale vengono utilizzate diverse tipologie di leghe metalliche e leghe speciali, ognuna delle quali, però, deve poter soddisfare specifici requisiti di resistenza, peso e durabilità.
Ecco alcune delle leghe metalliche più comunemente impiegate:
Titanio
Il titanio è noto per la sua resistenza e leggerezza. Le leghe di titanio come il Ti-6Al-4V sono comunemente utilizzate in componenti critici, come parti del motore e parti strutturali degli aeromobili.
Acciaio inossidabile
Gli acciai inossidabili sono spesso utilizzati per le parti di aerei esposte agli elementi o per quei componenti che richiedono una resistenza superiore alla corrosione, come nei motori.
Leghe di magnesio
Le leghe di magnesio sono leggere ma forti e vengono utilizzate in parti non strutturali e altri componenti di aerei.
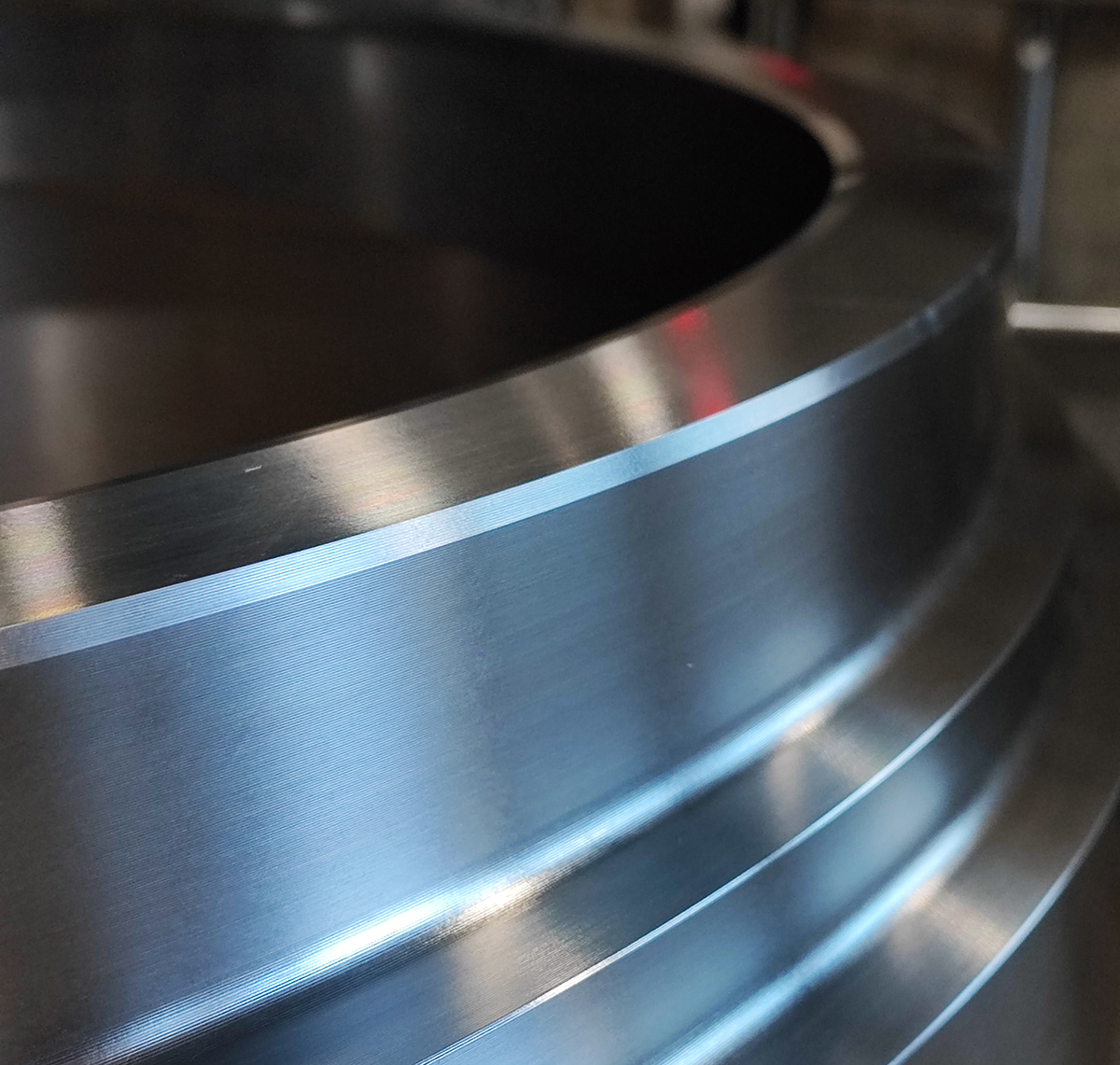
Compositi
Anche se non sono leghe metalliche, i materiali compositi sono ampiamente utilizzati nel settore aerospaziale. Combinano materiali come fibra di carbonio e resine, per creare componenti leggeri e resistenti.
Materiali avanzati
Il settore aerospaziale continua a sviluppare e adottare nuovi materiali avanzati, come leghe metalliche a memoria di forma, nanocompositi e materiali compositi avanzati, per migliorare le prestazioni e la durabilità degli aeromobili.
Alluminio
Le leghe di alluminio sono ampiamente utilizzate in molte parti degli aeromobili grazie alla loro leggerezza e resistenza alla corrosione. La lega 7075 è nota per la sua alta resistenza ed è spesso utilizzata per parti strutturali.
Superleghe
Queste leghe speciali sono progettate per resistere a temperature estreme e sforzi meccanici elevati. Alcuni esempi di tali materiali sono le leghe a base di nichel come Hastelloy e Waspaloy.
Inconel
L’Inconel è un altro materiale appartenente alla famiglia delle superleghe a base di nichel, notevolmente resistenti alle alte temperature, alla corrosione e all’ossidazione.
Queste leghe, oltre al nichel, appunto, contengono anche cromo e ferro e, in alcuni casi, anche altri elementi di lega come il molibdeno, il tungsteno e il niobio, che ne migliorano ulteriormente le proprietà.
Le leghe Inconel sono ampiamente utilizzate nell’industria aerospaziale e in altre applicazioni ad alta temperatura e corrosione, come parti di motori aeronautici, ad esempio le palette dei compressori.
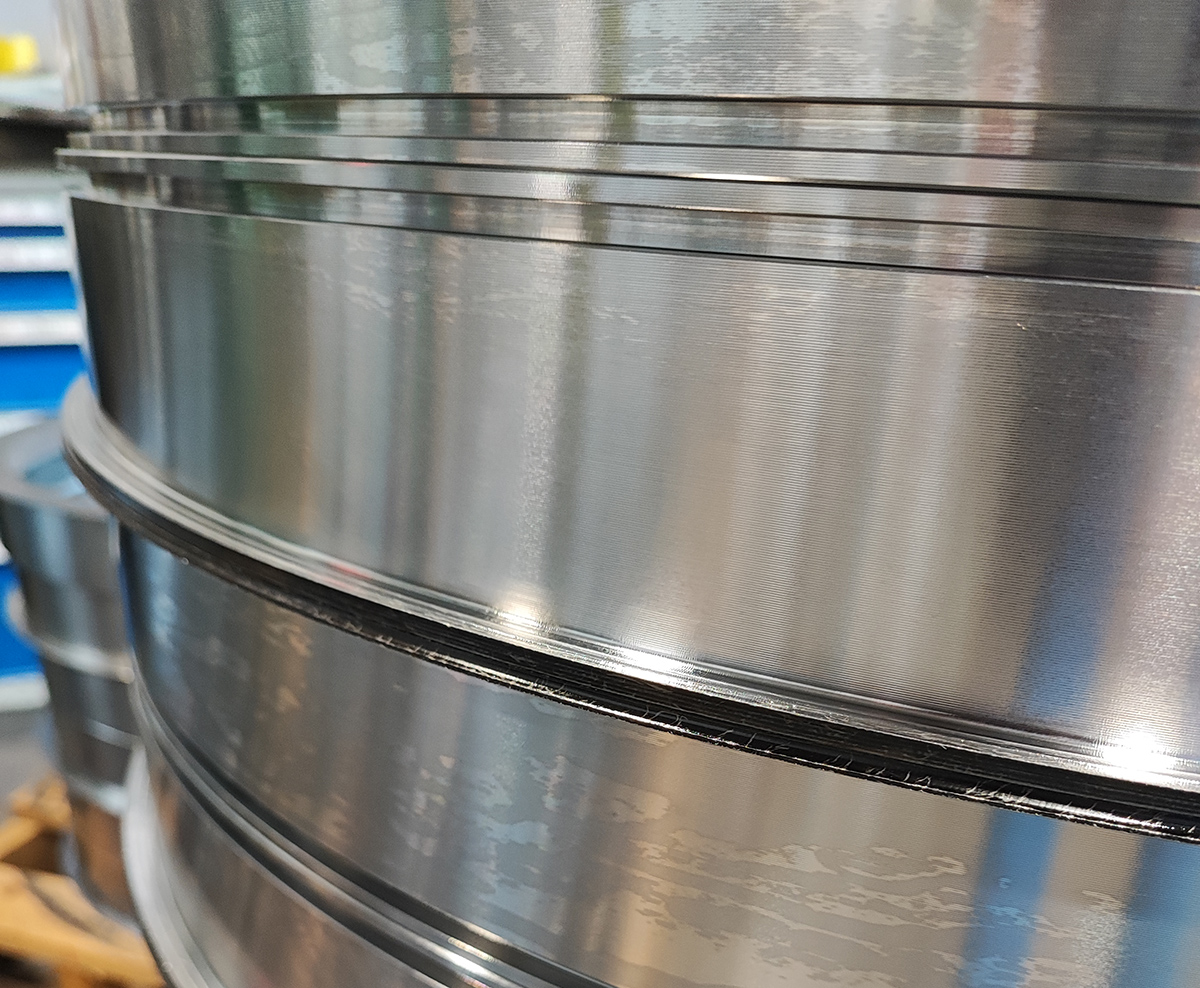
Perché le leghe per l’aerospaziale sono difficili da lavorare?
Le particolari ed eccezionali caratteristiche che contraddistinguono le leghe metalliche utilizzate in ambito aeronautico e spaziale, costituiscono in qualche modo anche un limite per questi materiali in termini di lavorabilità.
Ecco perché le aziende operanti nel settore devono necessariamente affidarsi a un partner specializzato come Lomec, in grado di lavorare leghe metalliche e leghe speciali per l’aerospace senza comprometterne le proprietà.
La lavorazione dell’Inconel, ad esempio, rappresenta una delle sfide più gravose e difficili che un’officina meccanica possa affrontare, per le particolari caratteristiche del materiale e per come queste ne condizionano la lavorazione.
Ad esempio:
Elevata durezza e resistenza
L’Inconel è noto per la sua elevata durezza e resistenza, specialmente a temperature elevate. Ciò ne rende la lavorazione meccanica difficoltosa e necessario l’impiego di strumenti e attrezzature dedicate, particolarmente resistenti e di alta qualità.
Tendenza all’indurimento a freddo
L’Inconel tende a indurirsi durante la lavorazione a freddo, aumentando progressivamente la difficoltà dell’operazione. Questo richiede un controllo attento delle temperature di lavorazione e può rendere necessarie delle procedure di riscaldamento intermedio al fine di ammorbidire il materiale.
Usura degli utensili
A causa della sua durezza, l’Inconel può causare un’usura significativa degli utensili di taglio e delle attrezzature di lavorazione, rendendone così necessaria la sostituzione frequente, da cui derivano costi aggiuntivi.
Bassissima conducibilità termica
L’Inconel ha una bassissima conducibilità termica, il che significa che il calore generato durante la lavorazione tende ad accumularsi nella zona di taglio. Questo può portare a problemi di surriscaldamento, deformazione e deterioramento degli utensili.
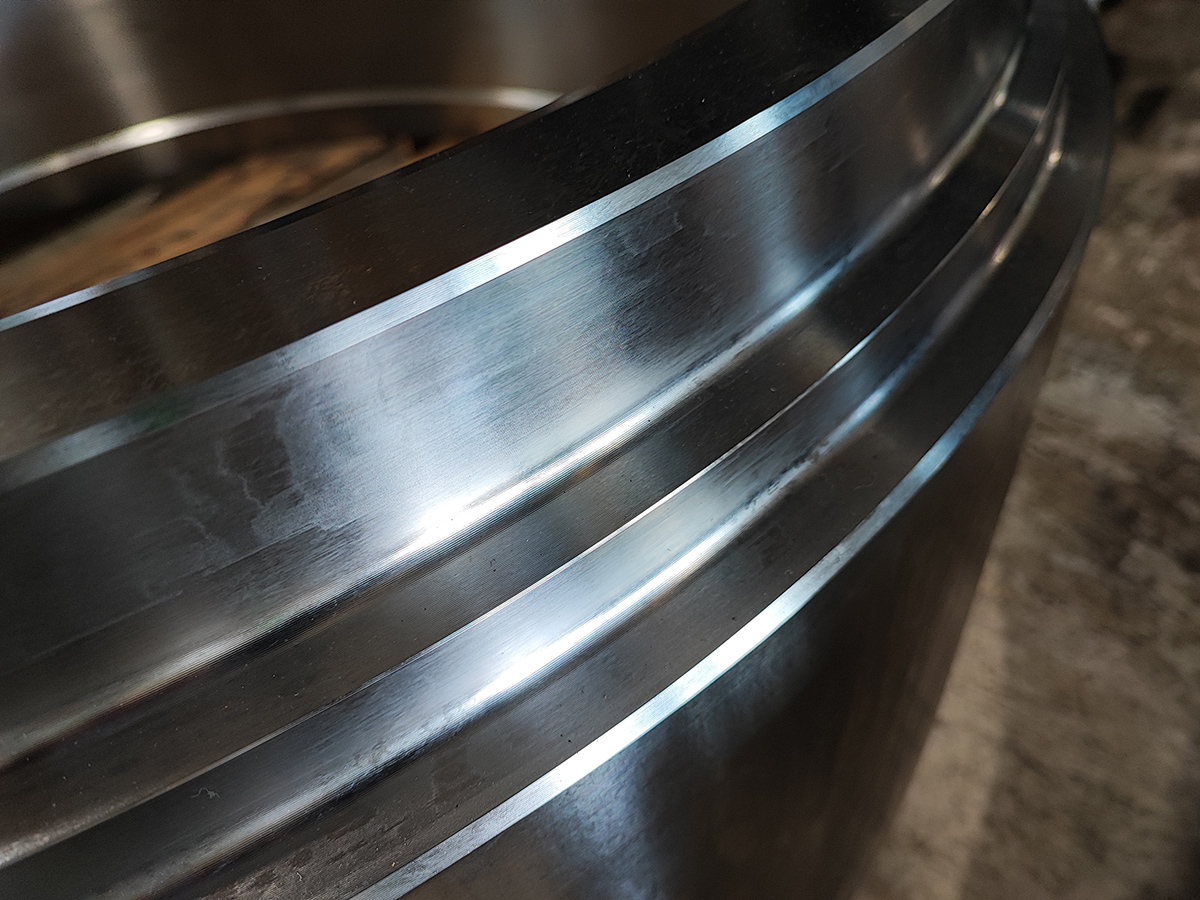
Tendenza all’incrudimento delle macchine
La lavorazione dell’Inconel può causare un deterioramento delle macchine utilizzate a causa delle elevate pressioni e dei carichi applicati. Questo può richiedere una manutenzione più frequente delle macchine.
Tolleranze strette e finiture superficiali
La lavorazione dell’Inconel richiede spesso tolleranze strette e finiture superficiali precise, difficili da ottenere a causa delle sue caratteristiche materiali.
Per affrontare queste sfide, Lomec utilizza strumenti di taglio di alta qualità, progettati specificamente per la lavorazione dell’Inconel.
Lavorazione che in azienda è affidata a un team di operatori esperti, specializzati nel maneggiare questo particolare materiale, applicando tecniche di raffreddamento e lubrificazione speciali, per prevenire surriscaldamenti e ottenere un prodotto finito della massima qualità possibile.
Contattaci per avere maggiori informazioni.